keep_hope_alive Premium Member
Acoustics Engineer
Welcome to the audio and acoustic build log for my 2023 SS Camaro. This will be long, with a lot of photos, because that is how all of my build logs are.
Here are some pics of the car, I went with a black exterior with gray rally stripes and a gray interior:
It is a daily driver, even in northern IL winters using Blizzak winter tires
My 2014 Accord Sport with 220,000 miles as my previous daily driver and my new daily driver.
I also designed and 3D printed a custom SS emblem for the front grille
I ordered this car to my desired specification in May of 2022, it was built in August of 2022 and I took delivery in September of 2022. One year and 20,000 miles later, I am finally able to dissemble the car to do acoustical treatments and properly setup a sound system. I ordered the 1SS package because it included the 8” infotainment IOS interface but without Bose. As a result, I have a full-range signal out of the front that I can use. The plan is my typical equipment, transferred from my 2014 Accord: Hertz Mille front and sub stage and JL VXi (or MVi) amplifiers for the built-in DSP. Acoustical treatments will be by Resonix for their quality and performance.
As with all of my builds, step one is disassembly. To do this safely, I purchased a subscription to ACDelcoTDS and used the access to the dealer service information to download instructions to disassemble all of the interior panels, as well as electrical schematics for most of the systems in the car. The disassembly instructions allow me to know exactly where fasteners and clips are, so nothing gets broken during the process.
Disassembly
This is a sports car, no doubt, but a budget sports car. The budget aspect is very apparent when tearing into the interior. The interior plastic is cheap and the fasteners at the rear are mostly plastic push-in clips that you destroy when removing them. There are a lot of rattle opportunities in the back as a result. The metal is very resonant, and a lot of treatment will be required prior to putting anything behind the B-pillar.
The battery is in the rear passenger corner, which is fairly handy. There are 60A and 100A outputs available, which will match the amplifier selections nicely. The driver’s side rear corner is mostly empty and JL makes a StealthBox for this location. I plan on using this space for the JL amplifiers, keeping them fully hidden behind the factory side panel.

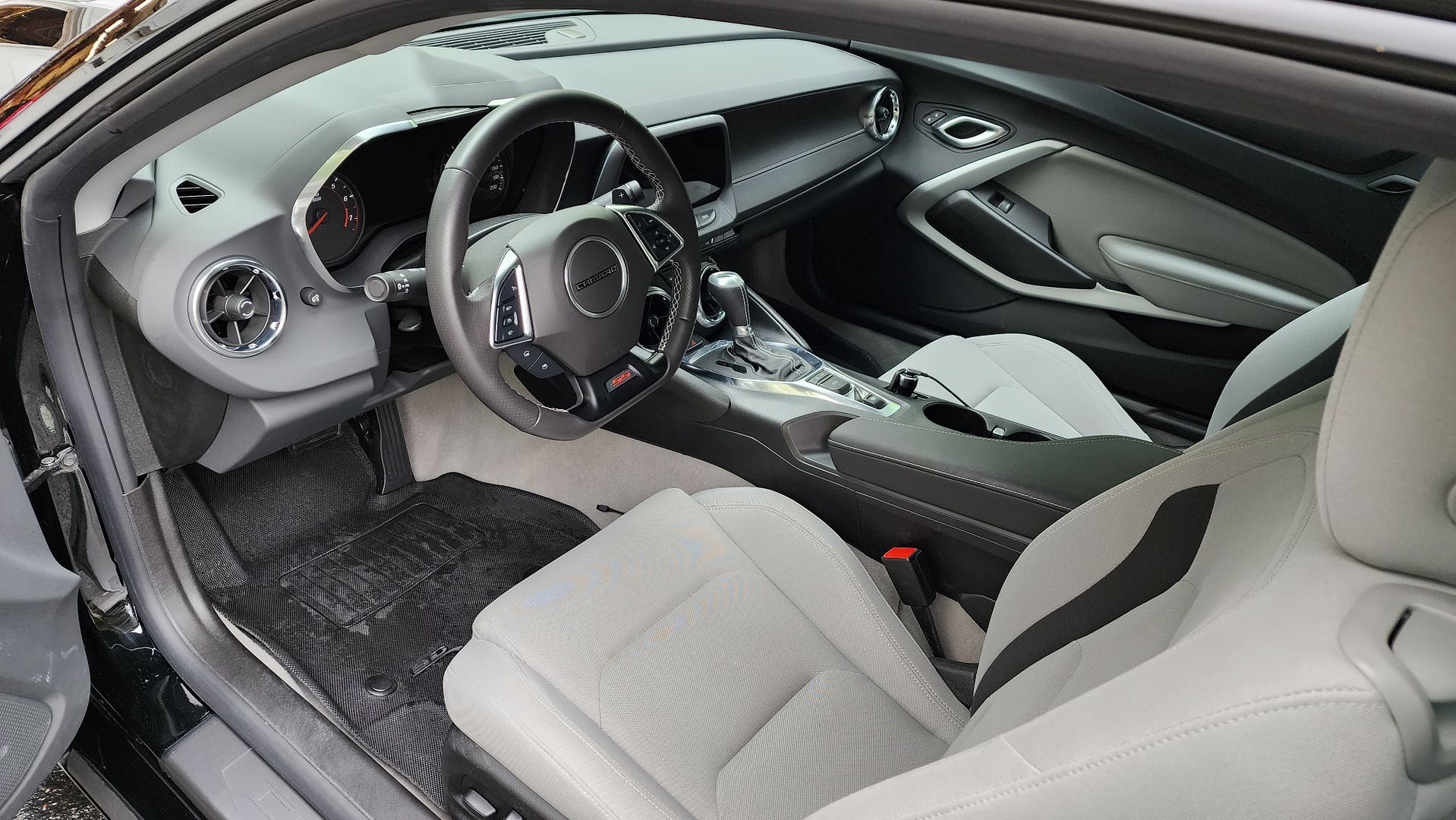
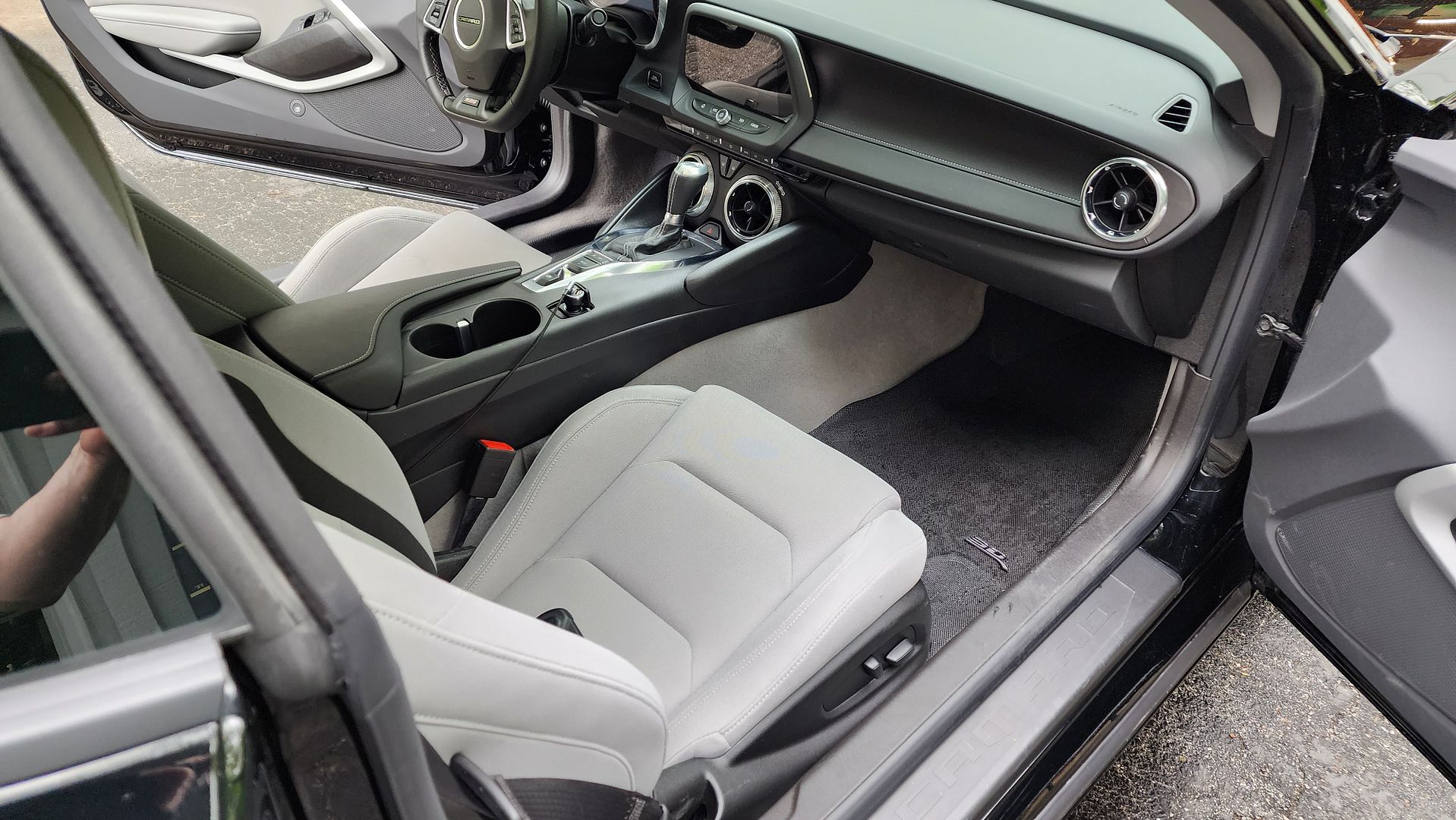
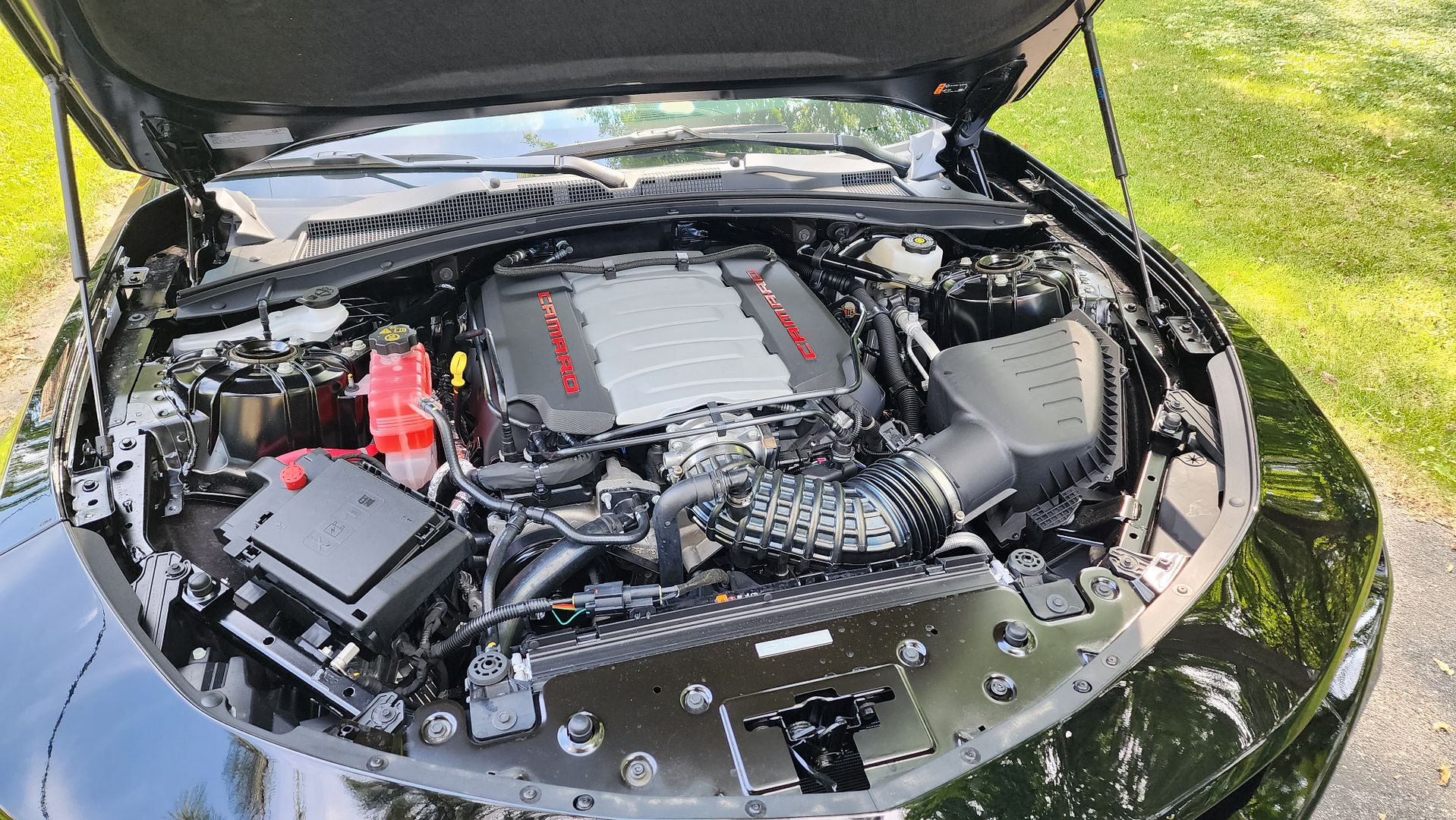
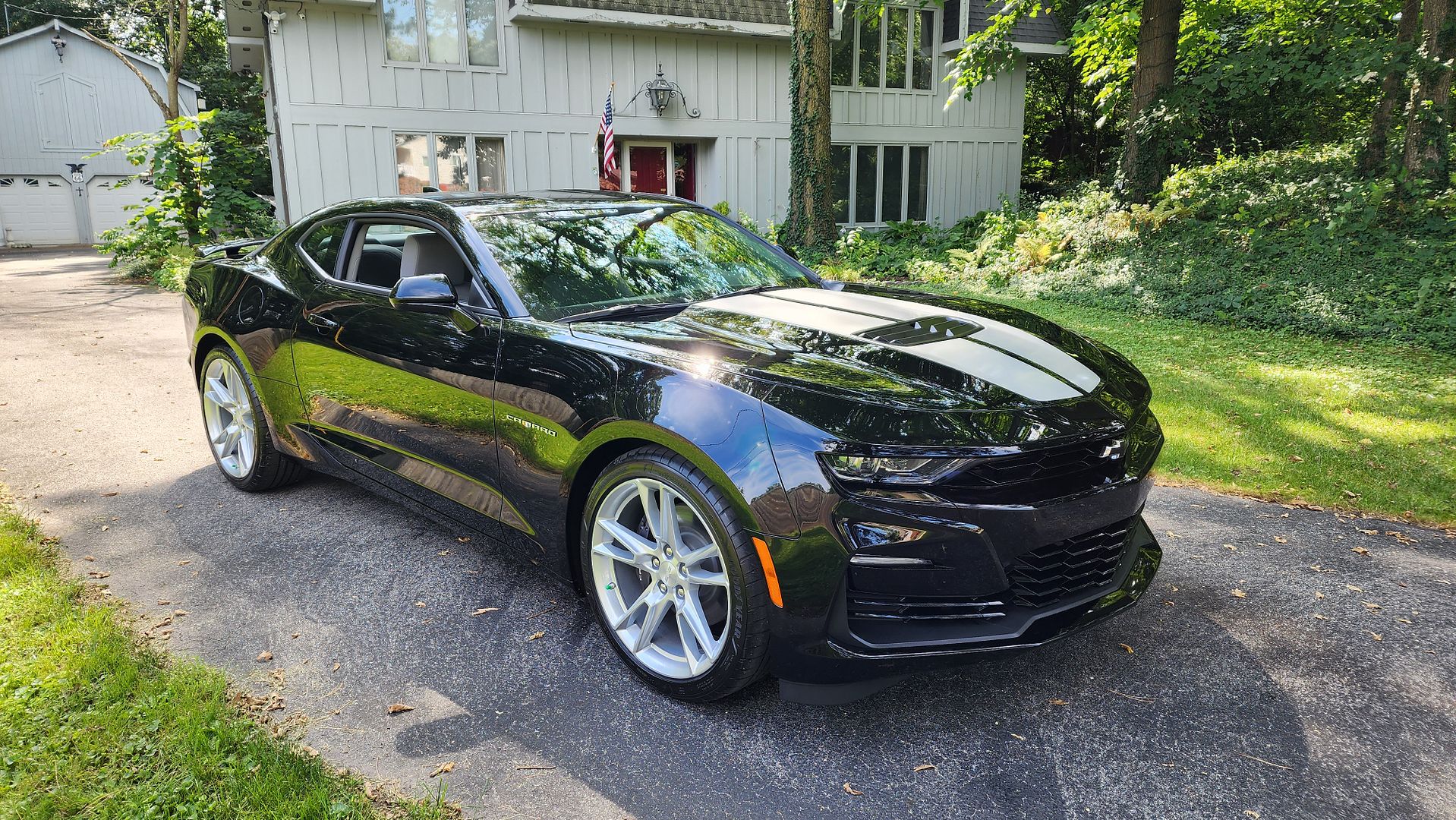
It is a daily driver, even in northern IL winters using Blizzak winter tires

My 2014 Accord Sport with 220,000 miles as my previous daily driver and my new daily driver.
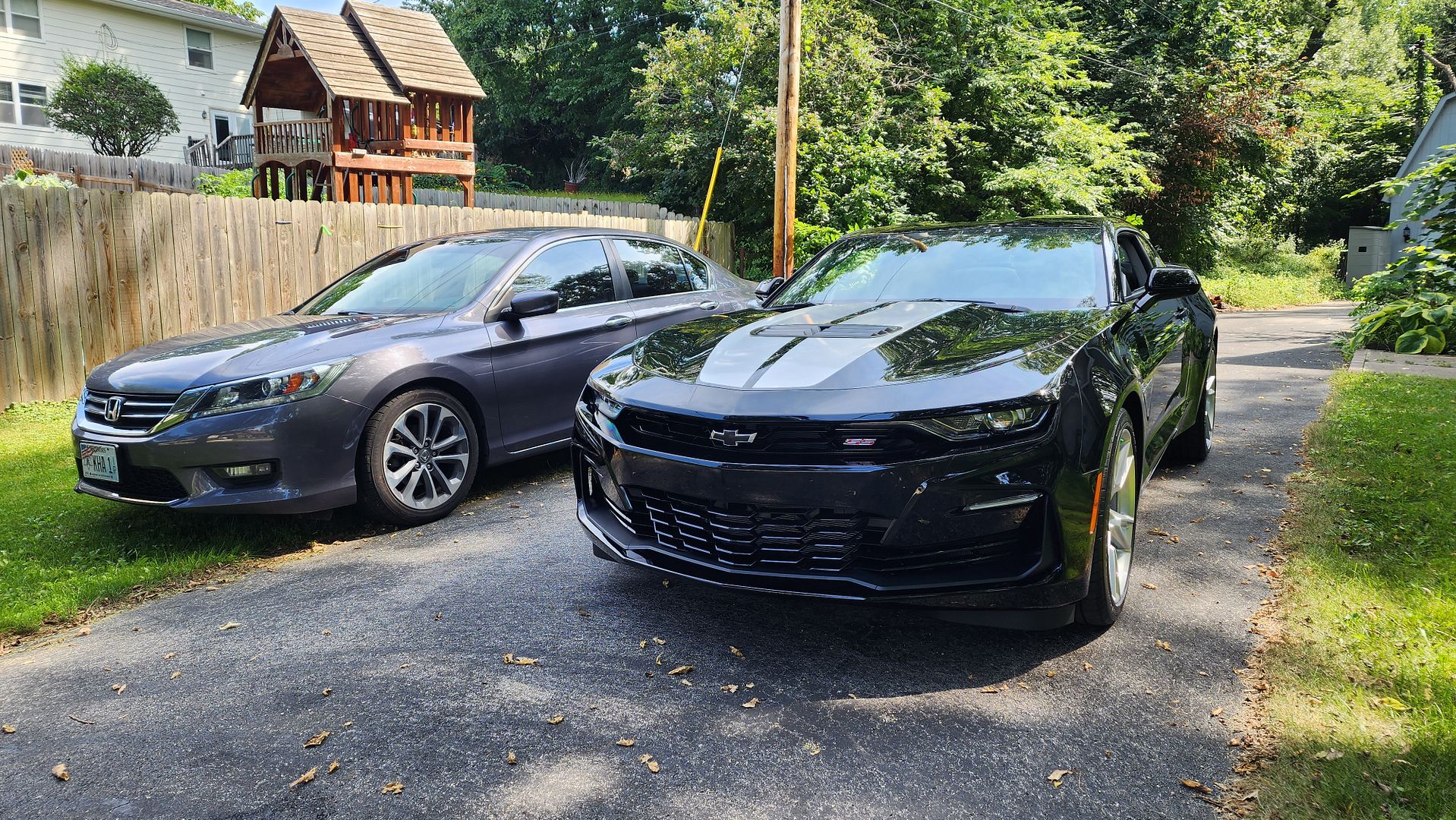
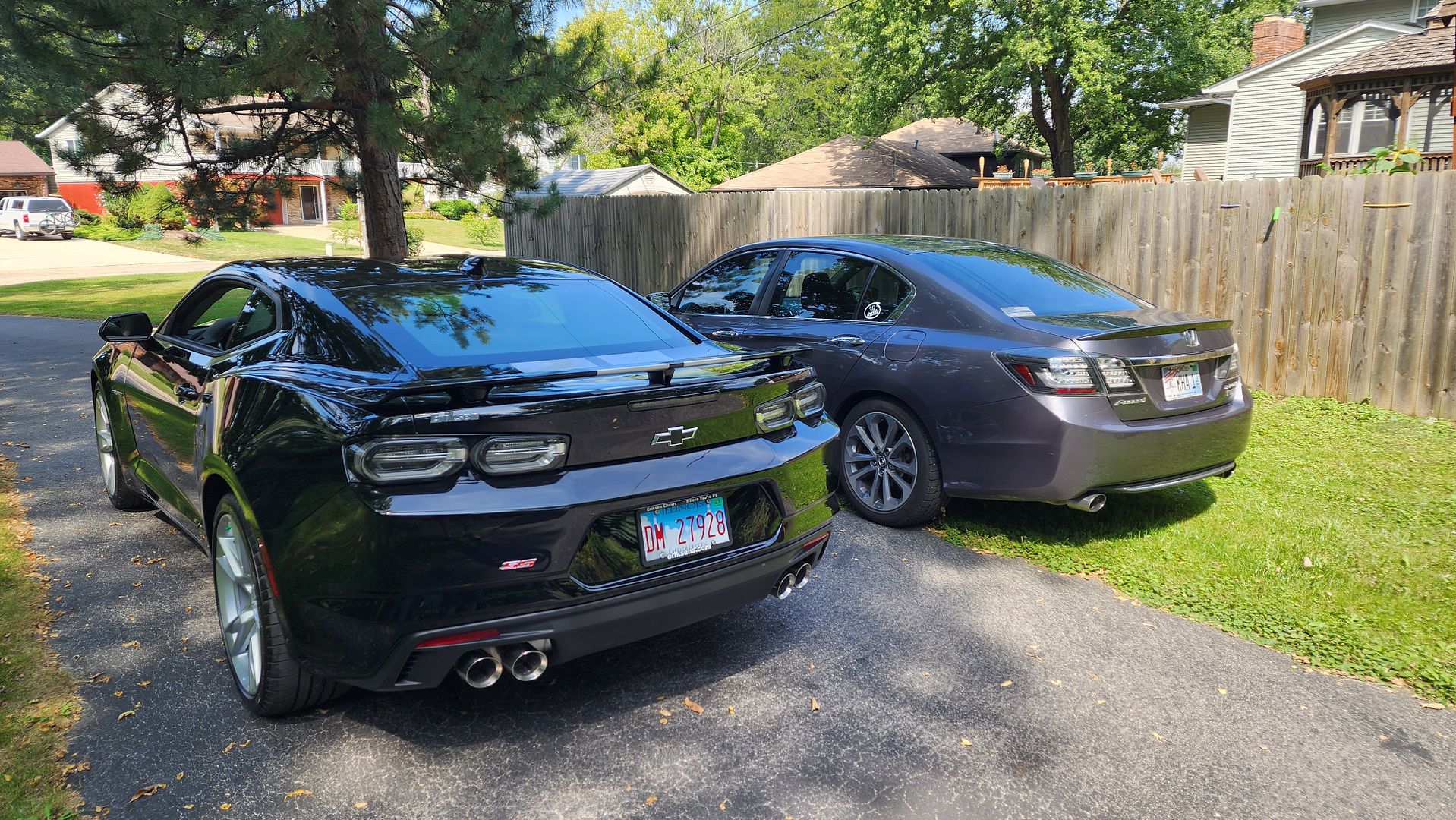
I also designed and 3D printed a custom SS emblem for the front grille
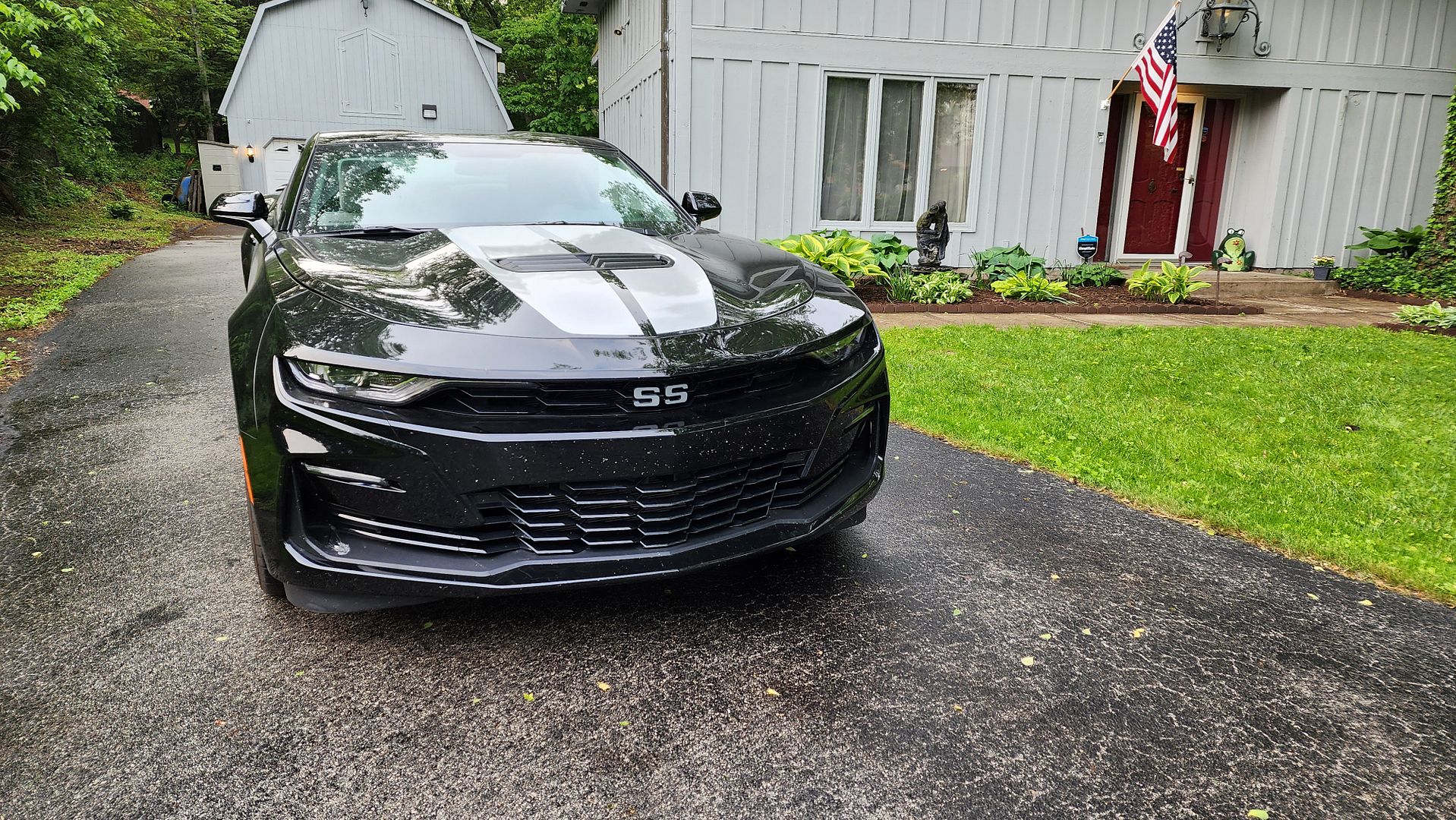
I ordered this car to my desired specification in May of 2022, it was built in August of 2022 and I took delivery in September of 2022. One year and 20,000 miles later, I am finally able to dissemble the car to do acoustical treatments and properly setup a sound system. I ordered the 1SS package because it included the 8” infotainment IOS interface but without Bose. As a result, I have a full-range signal out of the front that I can use. The plan is my typical equipment, transferred from my 2014 Accord: Hertz Mille front and sub stage and JL VXi (or MVi) amplifiers for the built-in DSP. Acoustical treatments will be by Resonix for their quality and performance.
As with all of my builds, step one is disassembly. To do this safely, I purchased a subscription to ACDelcoTDS and used the access to the dealer service information to download instructions to disassemble all of the interior panels, as well as electrical schematics for most of the systems in the car. The disassembly instructions allow me to know exactly where fasteners and clips are, so nothing gets broken during the process.
Disassembly
This is a sports car, no doubt, but a budget sports car. The budget aspect is very apparent when tearing into the interior. The interior plastic is cheap and the fasteners at the rear are mostly plastic push-in clips that you destroy when removing them. There are a lot of rattle opportunities in the back as a result. The metal is very resonant, and a lot of treatment will be required prior to putting anything behind the B-pillar.
The battery is in the rear passenger corner, which is fairly handy. There are 60A and 100A outputs available, which will match the amplifier selections nicely. The driver’s side rear corner is mostly empty and JL makes a StealthBox for this location. I plan on using this space for the JL amplifiers, keeping them fully hidden behind the factory side panel.
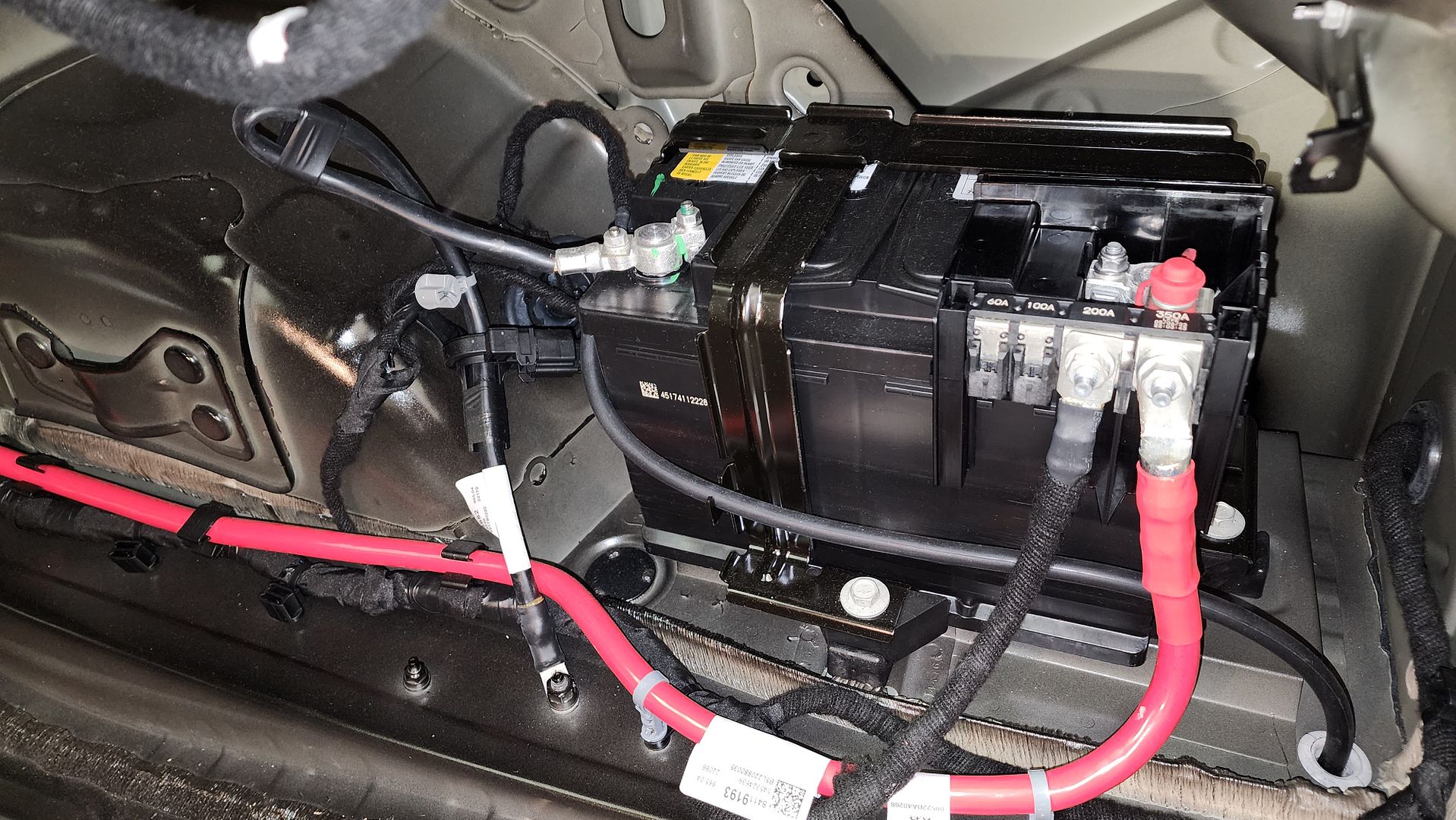
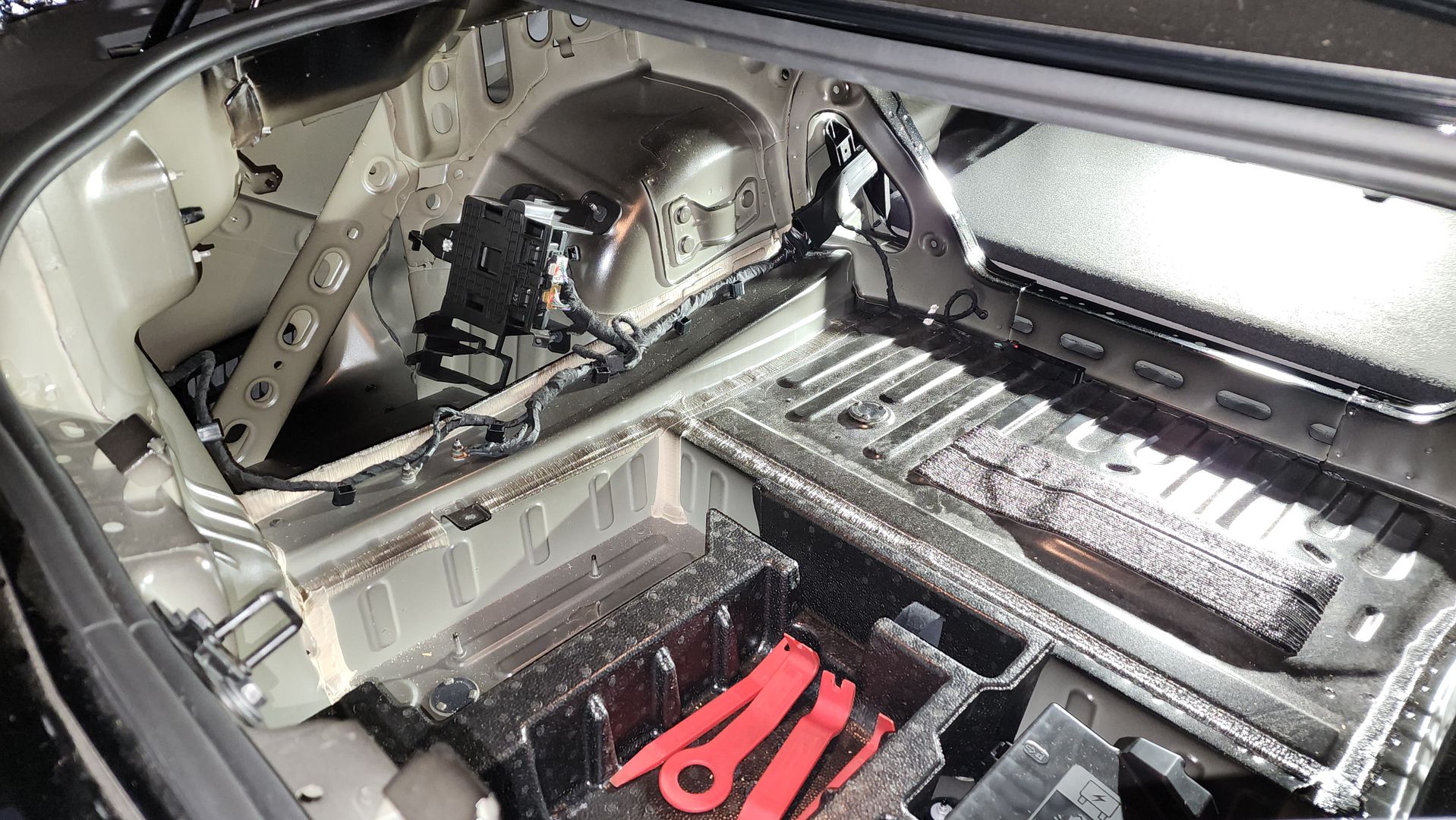
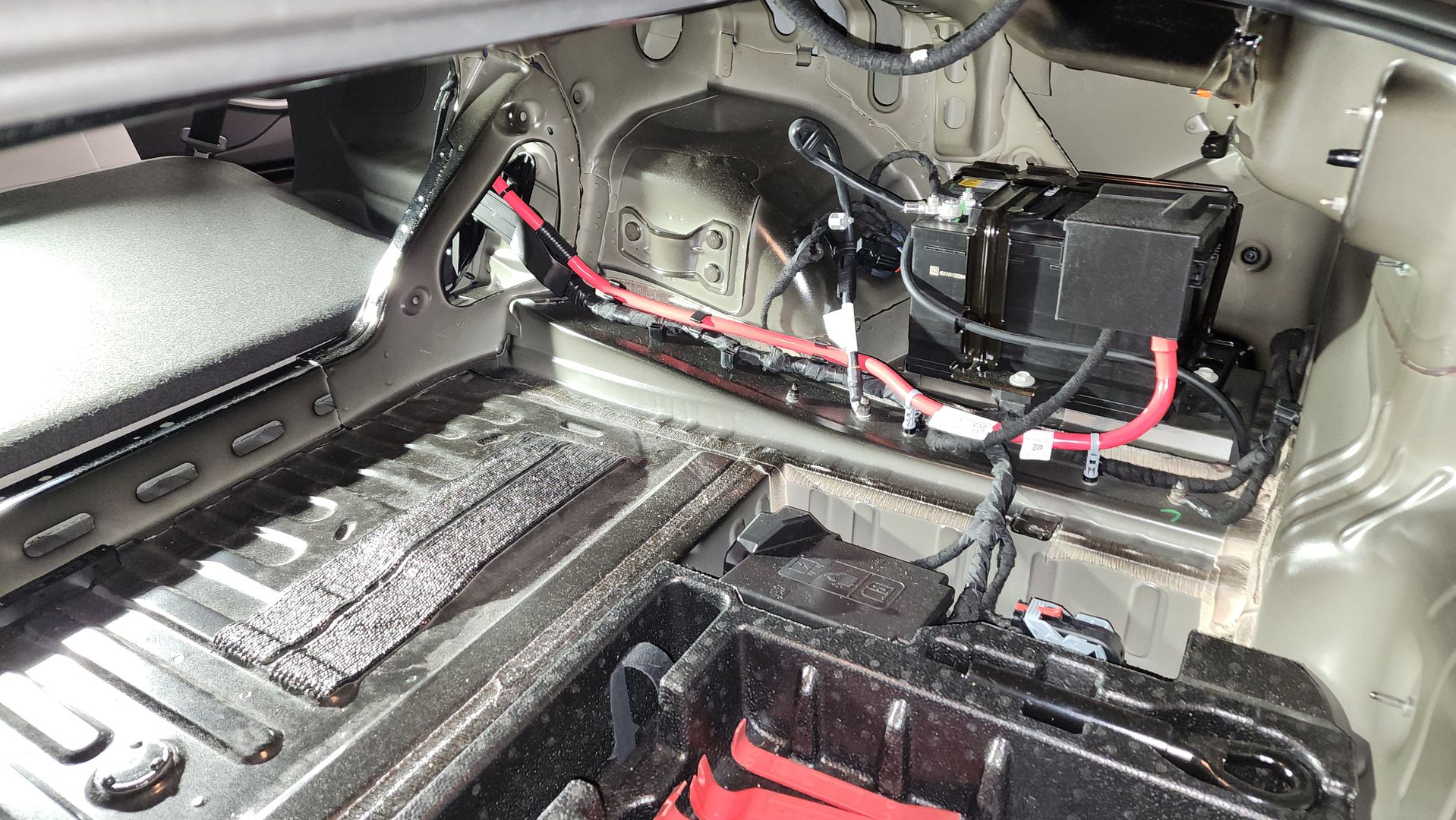
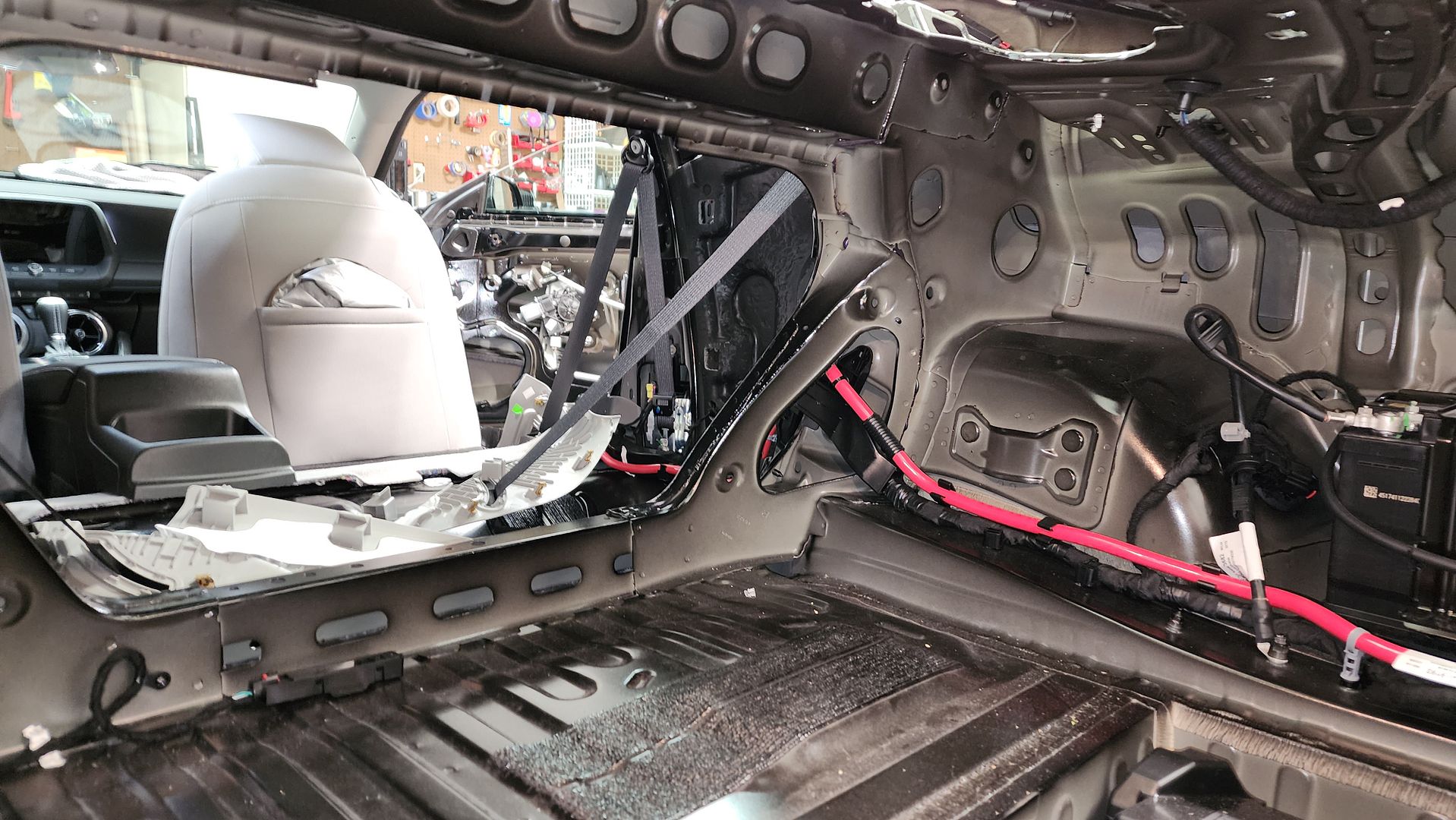
- Build Photo
- Okay
Attachments
Last edited: